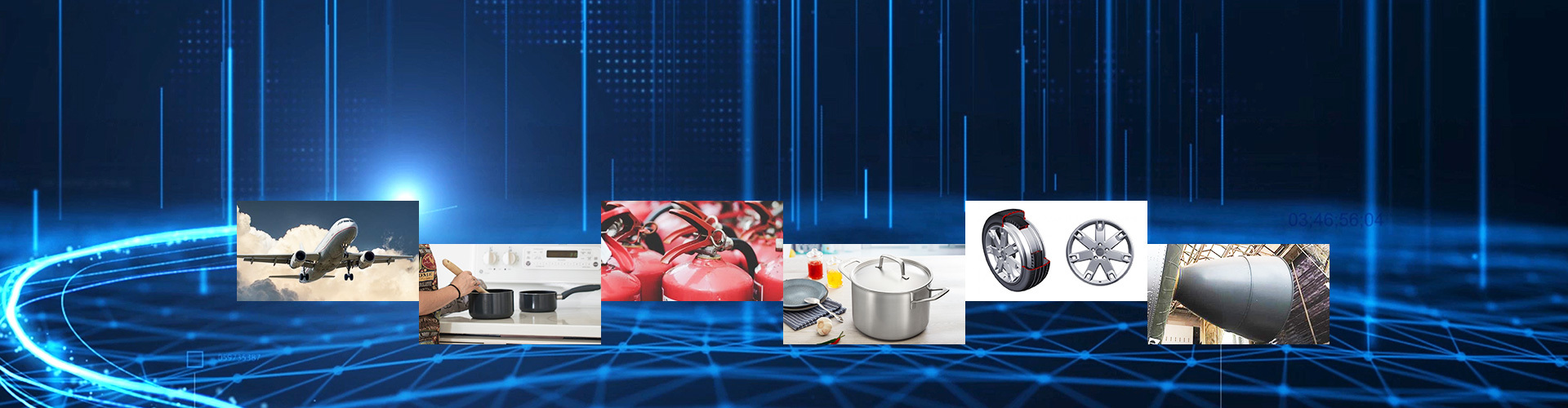
Flanging and crimping
According to the shape and size of the forming parts, the method of rotating the flange at the end of the tube with a rotating wheel is called flanging. Flanging is divided into outer flanging and inner flanging. The rotary wheel used is generally a flanging wheel composed of circular arc and cylindrical. When spinning, it is first pushed to the edge of the workpiece through the arc segment to turn it into an arc, and then the cylindrical segment is used to film and flatten it into a flange-shaped flange.
Curling forming the end of the spinning part is rounded to enhance the rigidity of the workpiece, and sometimes it can be used as a decoration to beautify the shape of the workpiece. The curling is formed by pressing the edge of the spinning piece with a curling wheel with a circular groove on the outer periphery. Depending on the shape of the edge curl, the corresponding wheel can be used for processing.
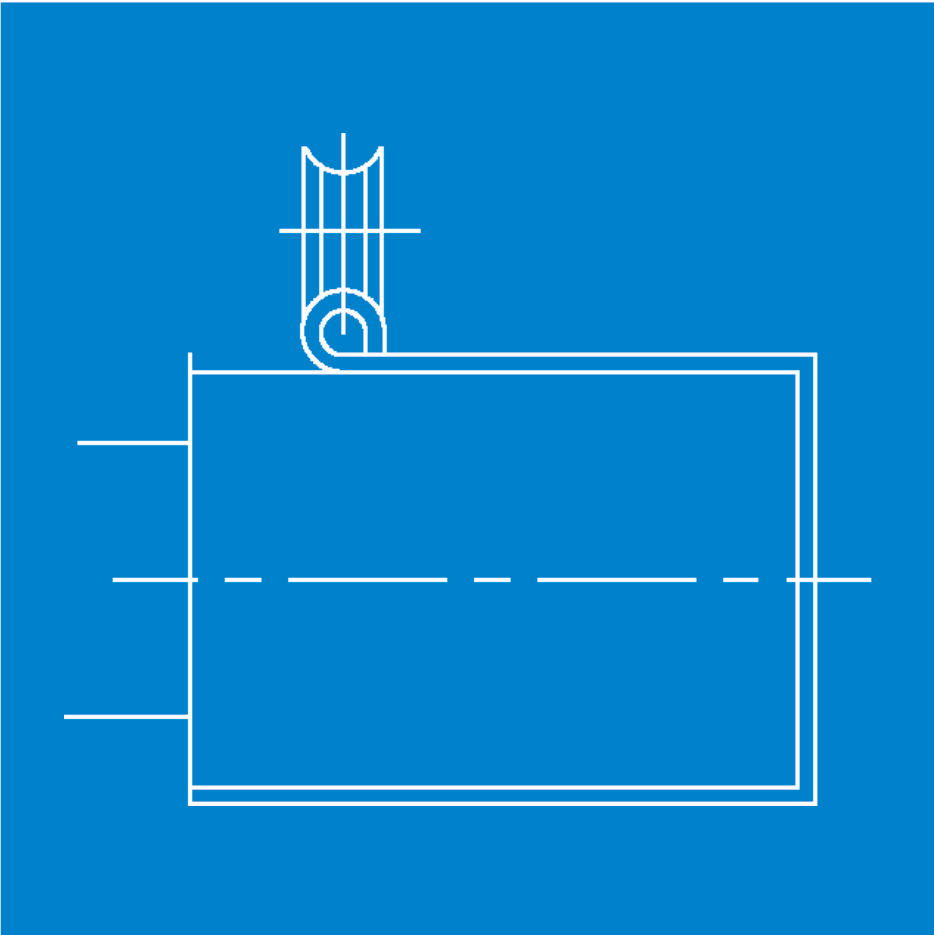
Generally, the crimping is required to have a certain degree of sealing, good anti-leakage performance and impact resistance, so as to ensure that the steel drum can withstand various forms of collision and drop in transportation and storage. In the process of flanging, the steel barrel is rolled by the flanging machine, which forces the barrel body and the top and bottom of the barrel to curl tightly. In order to make the barrel body and the barrel top and bottom curl and deform during rolling, the flanging machine makes the crimping process step by step to minimize the deformation resistance.
Contact Us

Company address: No.1 Xinqi Road, Xiage Town, Xianju, Taizhou City, Zhejiang Province

Address of R & D Center: No. 500, Zhongcun Industrial Park, Binhai Town, Wenling City, Taizhou City, Zhejiang Province
COOKIES
Our website uses cookies and similar technologies to personalize the advertising shown to you and to help you get the best experience on our website. For more information, see our Privacy & Cookie Policy
COOKIES
Our website uses cookies and similar technologies to personalize the advertising shown to you and to help you get the best experience on our website. For more information, see our Privacy & Cookie Policy
These cookies are necessary for basic functions such as payment. Standard cookies cannot be turned off and do not store any of your information.
These cookies collect information, such as how many people are using our site or which pages are popular, to help us improve the customer experience. Turning these cookies off will mean we can't collect information to improve your experience.
These cookies enable the website to provide enhanced functionality and personalization. They may be set by us or by third-party providers whose services we have added to our pages. If you do not allow these cookies, some or all of these services may not function properly.
These cookies help us understand what you are interested in so that we can show you relevant advertising on other websites. Turning these cookies off will mean we are unable to show you any personalized advertising.