Reducing diameter spinning
The use of spinning tools to make the rotating body hollow or tubular blank radial local spinning compression to reduce its direct forming method.
The shrinking process is to clamp the blank concentrically into an appropriate core die (such as solid core, combined or coreless die), and expose the part to be formed to the outside of the fixture. When the main shaft drives the blank to rotate, the rotating wheel is made to reciprocate according to the specified shape trajectory according to the adopted control mode, gradually reducing the diameter of the blank, and then obtaining a spherical part with waist drum shape or closed.
When shrinking, in order to avoid wrinkling and cracking of the workpiece, the process is divided into several passes or processes according to the ratio of diameter before and after forming, that is, the rotary wheel should make multiple reciprocating movements, and the feed rate of each pass should be determined according to the ratio of diameter. For the specific case of forming parts of different shapes without materials, it is sometimes necessary to replace the core mold several times and carry out intermediate heat treatment. If necessary, it should be retracted under heating conditions.
In the wall thickness of the workpiece shrinkage zone, there are usually three situations: constant wall thickness, thinning and increasing wall thickness.
Wall thickness changes are mainly related to the degree of shrinkage and material properties. The above three situations also occur when the open end of the hollow workpiece is retracted.
According to the shape, material and quality requirements of the workpiece, different production methods can be used.
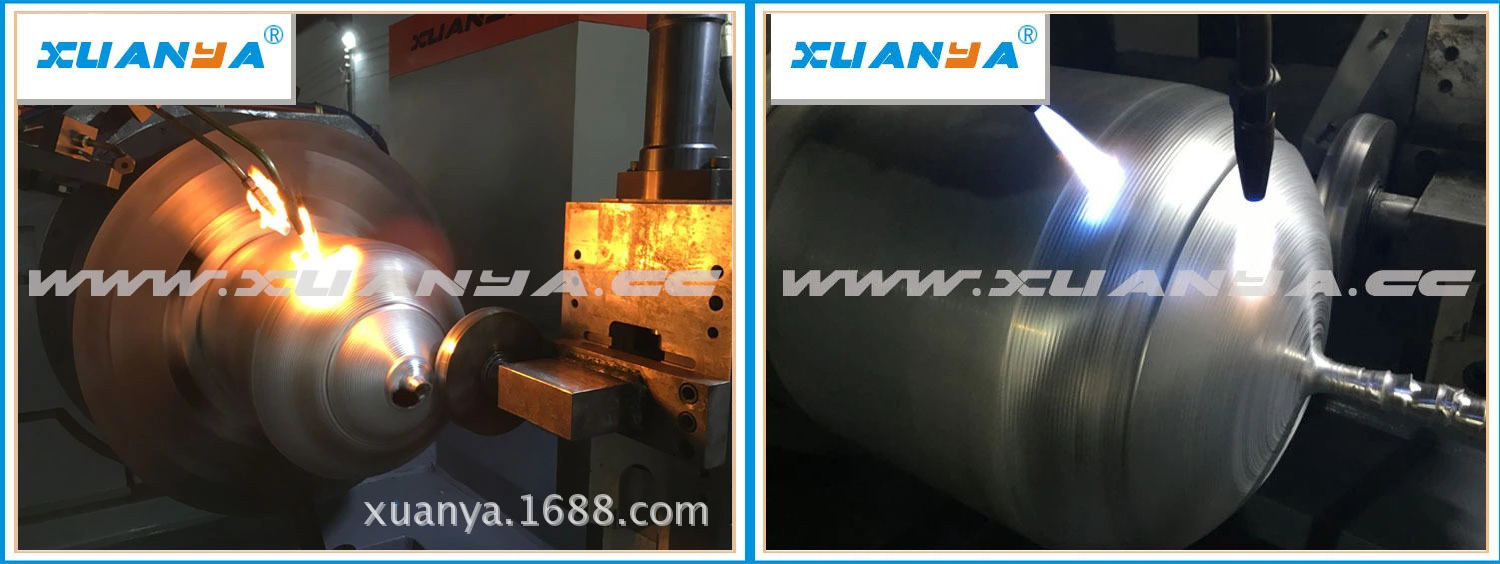